Essential Reasons for Immediate Cleaning and Maintenance of Tracks and Rollers
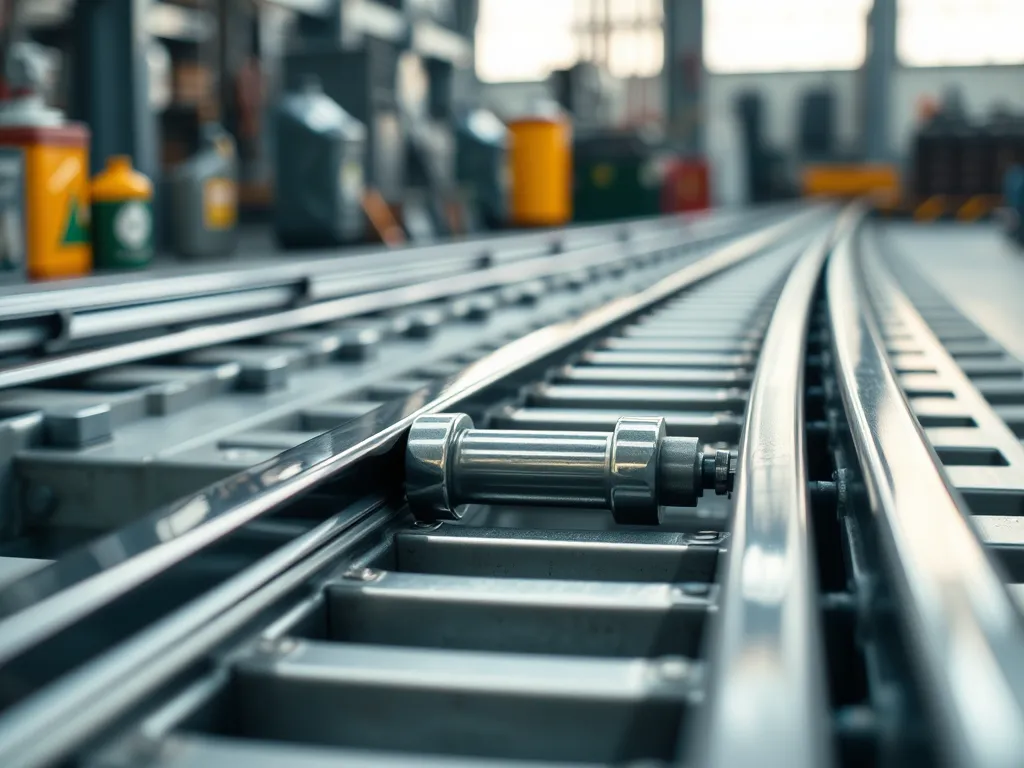
The Need for Immediate Cleaning and Maintenance of Tracks and Rollers
The need for immediate cleaning and maintenance of tracks and rollers cannot be overstated. Regular maintenance ensures that machinery operates smoothly and efficiently, preventing unexpected breakdowns that can lead to costly downtimes. These components, whether in manufacturing, construction, or transport, are critical to the overall functionality of equipment. Therefore, insightful adherence to their upkeep can significantly enhance productivity, as well as ensure operational safety.
If you're hearing unusual grinding noises, it's time to inspect your garage door system for potential issues.
Aside from keeping machinists productive, neglecting the cleaning and maintenance of tracks and rollers can lead to serious mechanical issues over time. Dirt, debris, and grease accumulation can hinder the proper movement of rollers along the tracks, producing friction and wear. This means more repairs and replacement costs as components fail prematurely. Understanding the need for immediate cleaning and maintenance of tracks and rollers is vital for any business that relies on these systems.
Furthermore, the need for immediate cleaning and maintenance of tracks and rollers has repercussions for workplace safety. Defective machinery not only affects output but also puts employees at risk. Equipment failures can result in accidents that lead to injuries or even fatalities. Thus, consistent and thorough maintenance routines are essential to create a safe working environment. Companies should prioritize this aspect as part of their health and safety policies.
To effectively implement a cleaning and maintenance regime, it is essential to develop a systematic approach. This involves scheduling regular checks, establishing cleaning protocols, and incorporating these practices into daily operational procedures. This can not only minimize disruptions during peak production times but also serve to foster a workplace culture that emphasizes responsibility towards shared equipment.
In summary, the need for immediate cleaning and maintenance of tracks and rollers is a critical aspect of operating machinery across various industries. Regular cleaning and maintenance benefit not only the lifespan of equipment but also the safety and productivity of staff. Adopting best practices in this area can serve to ensure that operations run smoothly and efficiently, mitigating risks that come with neglect.
Importance of Regular Maintenance of Tracks and Rollers
Regular maintenance of tracks and rollers brings forth numerous benefits, chief among them being the optimization of performance. Clean tracks and rollers provide smoother operation and enhance the overall efficiency of machinery. As debris and contaminants are removed, the risk of mechanical issues is considerably lowered, resulting in fewer interruptions in the workflow.
Moreover, consistent maintenance contributes significantly to the lifespan of equipment. By routinely cleaning and checking these components, potential issues can be addressed before they escalate into severe problems. This proactive approach ensures that machinery remains operational for a longer period, thus maximizing the return on investment and reducing the frequency of replacements.
Performing a garage door repair can be a difficult operation if you're not familiar with the mechanisms involved.
Preventive maintenance also leads to cost savings in the long run. Investing time and resources in cleaning and regular maintenance may seem tedious initially, but the reduction in repair costs and increased productivity generated through this diligence ultimately saves money. Companies can avoid the financial pitfalls associated with emergency repairs, downtime, and production delays by adopting a regular maintenance schedule.
Regular maintenance can prevent visible debris accumulation in your garage, ensuring both functionality and safety.
Safety Risks Associated with Neglected Tracks and Rollers
Common accidents in workplaces often stem from dirty or poorly maintained tracks and rollers. Equipment that fails to function correctly can result in erratic machinery movements, leading to physical injuries among employees. Ensuring that tracks and rollers are kept clean mitigates these risks and fosters a safer environment.
Additionally, maintenance reduces workplace hazards by identifying and addressing issues before they can cause harm. Regular checks allow for the discovery of wear and tear or misalignments in tracks that can lead to failures during operation. By adequately maintaining these systems, employers contribute to a safer work environment and demonstrate a commitment to employee well-being.
Furthermore, there are regulatory standards that mandate the upkeep of tracks and rollers. Safety guidelines stipulated by health and safety organizations require regular inspection and maintenance of equipment to prevent accidents. Non-compliance with these standards can result in legal repercussions, financial penalties, and reputational damage as a result of unsafe workplace conditions.
Techniques for Effective Cleaning of Tracks and Rollers
When it comes to cleaning tracks and rollers, employing best practices according to the material's characteristics is vital. Different materials may require specific methods to avoid damage while ensuring effective cleaning. For instance, softer surfaces might benefit from gentle scrubbing, while metal components may necessitate more robust cleaning agents.
Using appropriate cleaning agents and tools is essential for the effectiveness of the cleaning process. Abrasives should be avoided unless specifically designed for the material in question, as these can scratch surfaces or lead to corrosion. The right selection of tools such as brushes, vacuums, and pressured air systems can enhance the cleaning process and ensure that no debris remains.
It is equally important to establish a cleaning frequency tailored to operational conditions. For high-use scenarios, weekly cleaning sessions may be warranted, whereas less frequently used equipment may only need monthly or bi-monthly cleaning. This understanding of usage patterns helps develop an effective maintenance strategy which keeps tracks and rollers in prime condition while maximizing productivity.
Role of Technology in Track and Roller Maintenance
Innovative tools are emerging to assist in tracking maintenance needs for tracks and rollers. Technologies such as condition monitoring systems can provide real-time data on the state of these components, alerting managers to necessary maintenance and cleaning schedules. This information can help companies stay ahead of potential issues that could cause failures.
Automation is also playing a significant role in aiding routine cleaning of tracks and rollers. Robotic cleaners can be deployed to reach difficult areas and adhere to strict cleaning protocols, reducing the need for manual labor while achieving high standards of cleanliness. This can further enhance productivity and ensure consistent upkeep.
Looking ahead, future trends in maintenance technology include the integration of artificial intelligence and machine learning, which hold the potential to predict maintenance needs based on patterns and historical data. Such advancements can streamline the maintenance process and significantly reduce risks associated with neglected tracks and rollers.
Case Studies on Track and Roller Maintenance
Successful cleaning initiatives across different industries indicate the immense benefits of maintaining tracks and rollers. For instance, a leading manufacturing facility implemented a rigorous cleaning routine and saw a 20% reduction in machinery downtime. This dramatic improvement showcased the value of prioritizing the upkeep of these critical components.
Conversely, lessons learned from maintenance failures highlight the risks of neglect. A construction firm suffered significant delays and financial loss due to a failure in regularly cleaning and maintaining their equipment, leading to several breakdowns and safety incidents. These experiences underscore the importance of all-encompassing cleaning and maintenance protocols.
Comparative analysis of different maintenance strategies reveals that organizations which proactively maintain tracks and rollers outperform those that reactive address issues as they arise. Evidence from various sectors shows that consistent upkeep translates into not just a safer work environment but also better throughput and operational efficiency.